VDP:
Variable Data Printing
Automatic creation of proof sheets and bill of deliveries
The Variable Data Printing (VDP) functionality – which is also part of its automation software packages – allows proofs, bills of delivery and other individualized documents to be generated automatically.
The process itself is very simple:
Based on artwork created by the customer and job details (like number of print runs, format, etc.) the system creates proof documents that can be afterwards sent automatically to the customer or manager for validation. If changes to the VDP template are required, these can be made directly and easily with the provided template editor.
What is important for tiled products, like poster or wallpaper printing, are a visual overview for assembling the product. For this OneVision´s VDP can create a miniature view of the product, so that technicians have an overall view of the final product for correct assembly.
Additional detachable parts can be placed around the poster, so that the customer or technician can see what was delivered without opening the product or get additional details for assembly.
Any structured data can be used as variable data and be used in the production process. This could be order numbers or also customer address data, which can be used for grouping of jobs.
It is even possible to process Braille automatically via VDP as shown in this success story from Christus Health
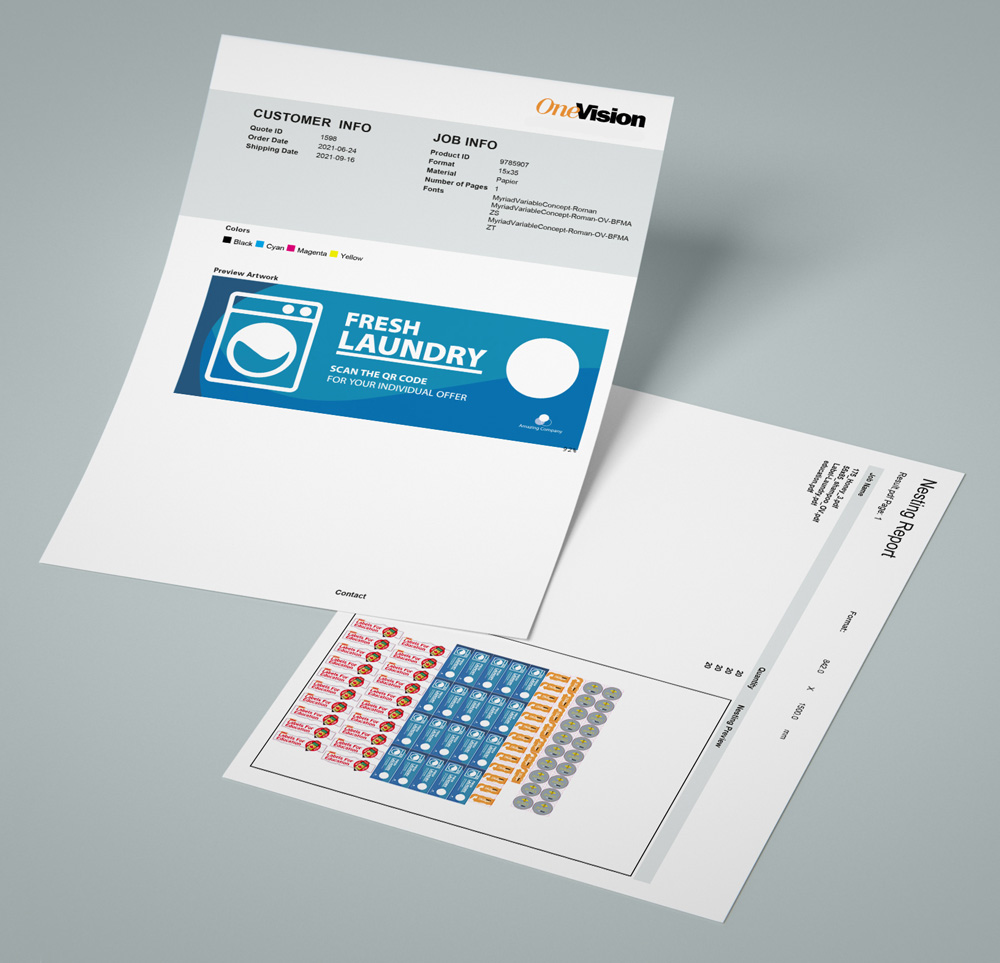
The advantages with Variable Data Printing (VDP) from OneVision
Gain a decisive competitive advantage with variable data printing:
- Precise production tracking thanks to barcode/QR code
- JobTicket enables automated print approval process
- Barcode/QR code-based assignment, incorrect assignments excluded
- Even Braille can be automated using VDP
Benefit from JobTicket and Barcodes
The JobTicket module, which is a part of OneVision workflow management system is taking the order information from XML or other source files. The information from that file is then translated into properties and the customers art file is being treated according to the specified information. Delivery date, name of the customer, email address, print substrate are only some examples which allow fully individual approach to the job. This allows to process each job individually based on the job ticket details. Additionally, each order can be tracked in the production. For this OneVision offers a product tracking functionality which is based on barcodes or QR-Codes.
Inserting and reading barcodes
OneVision’s automation software creates and reads barcodes allowing for scanning hardware to be able to automatically match different part of the order like different part of the book, brochure or magazine.
The barcodes can be added or read at any moment in the production process. They are a way to allow for spot checks and ensure for example in book on demand business the cover driven workflow where the cover printed on one press will match an insight printed on a different press.