Press release
Kongsberg and OneVision partnership showcases smart end-to-end finishing workflow
Collaboration underlines importance of hardware and software connectivity for efficient production
Regensburg/Kongsberg. New collaboration between Kongsberg Precision Cutting Systems (Kongsberg PCS) and OneVision Software. The leading digital finishing solutions manufacturer has partnered with one of the leading software solution providers for workflow automation to develop an integrated automation system. Delivering consistent data can maximize efficiency for digital finishing and ensure a smooth end-to-end workflow.
“Every converter wants their table to be running as close to 100% of the time and have as little downtime as possible,” said Koen Van Reybroeck, Product Manager at Kongsberg PCS. “They also want quality end products every time, regardless of who is operating the machine. The key to achieving this is consistency in the data sent to the machine and standardization based on the materials being produced.
“To get the best performance from our i-cut Production Console (iPC) and the table, the user wants to send additional metadata with the cut file,” explained Koen. “For example, the name of a substrate that will be used for producing the job. By focusing on the material, we can then standardize and optimize, automatically applying tools and settings that give the best cutting result. We refer to this as our ‘Material is Key’ way of working, ensuring a consistent file input quality, correct material and tooling presets and full unattended machine production.”
OneVision Business Development Manager, Sacha-Vittorio Paolucci, said that smooth end-to-end workflow ensures the consistency of files throughout the process. “The proven automation solutions from OneVision Software integrated with Kongsberg PCS cutting systems makes this possible,” he said. “The OneVision software can be easily integrated to automate and standardize all production steps from entry to finishing. With the smart connection to the Kongsberg cutting table, print and cut files are automatically checked and optimized.
“Market-leading nesting technology and cut line management prepares the files optimally for further finishing,” said Sacha-Vittorio. “This means that manual interventions thus become unnecessary, and processes are more efficient due to a substrate-saving production.”
Koen added that the focus of the integration is automation, both in file preparation and also on the cutting table itself. “With the Kongsberg-specific output formats and the integration of the Connect to Kongsberg module, OneVision users can now automatically push files to iPC and import them in a consistent way onto the cutting tables,” he said. “This also enables an operator to perform full, unattended production, freeing their time and further boosting efficiency and productivity.”
OneVision’s software solution also allows barcodes (QR) to be automatically added to the print file, helping speed up the production process as iPC can then load, prepare and start the different jobs automatically on the table, whether roll or sheet-fed production.
“This smart workflow offers standardization in iPC based on materials and tooling presets, delivering consistent cut quality independent from operator experience, as well as a more economical production for print service providers,” said Koen.
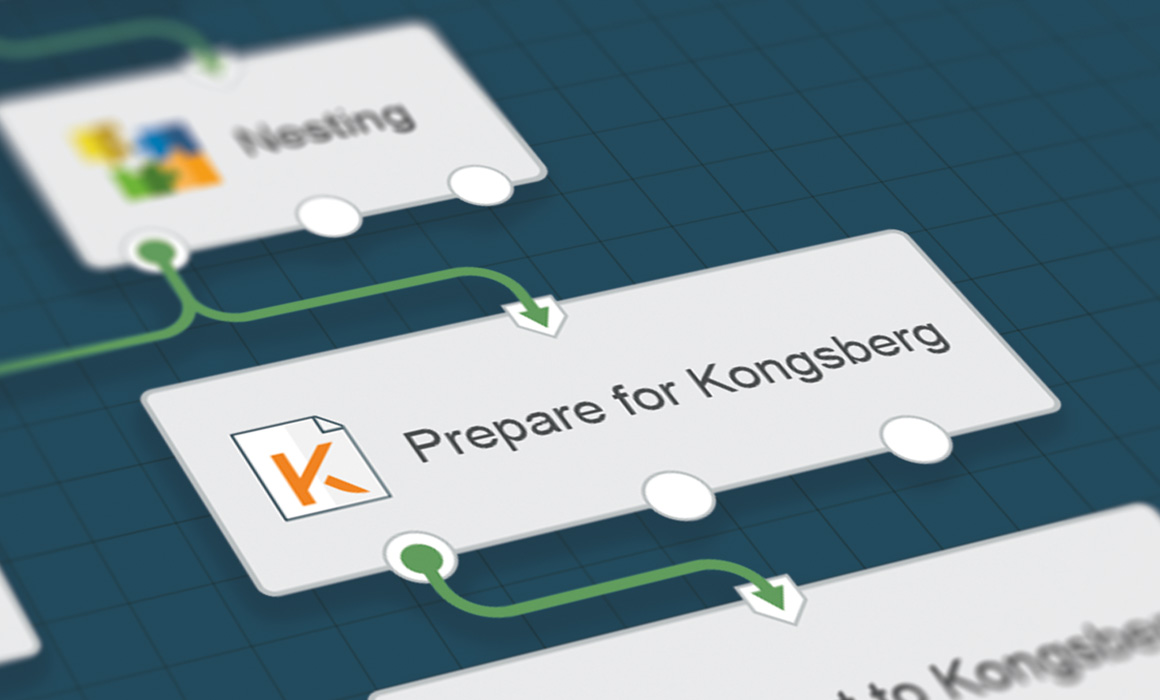
You are welcome to download the attached information material for your media activities.
Always up to date
For more news about OneVision and the latest trends in printing, please visit our NewsRoom.